Katanas, the famous Japanese swords, have long fascinated sword enthusiasts and history buffs alike. True icons of the samurai, these swords have a very specific swordsmanship technique, handed down from generation to generation by master swordsmiths. Let’s take a look at how these mythical swords are made.
Steel selection and preparation
Traditionally, Tamahagane is a type of steel used in the manufacture of Katanas. It is produced from iron ore, called iron sand, mixed with coal in a special furnace: the Tatara. It’s a brick furnace in which iron ore is heated to high temperatures to melt and purify it.
The purification process reduces the impurities in the steel, resulting in a high-quality alloy. The Tamahagane obtained is then broken into pieces, sorted according to its carbon content, and heated again to be ready for forging.
Today, we also use more carbon-rich and resistant steels such as T10 steel to obtain an even sharper, longer-lasting blade.
Forging: the heart of the process
The forging stage is undoubtedly the most crucial in the crafting of a katana. Swordsmiths take pieces of Tamahagane or other steel and heat them in a furnace to over 1300 degrees Celsius. Once heated, the steel is hammered and bent thousands of times to improve its molecular structure and strength.
This hammering and bending creates thousands of layers of steel, increasing the blade’s rigidity and flexibility. This process is known as laminating. After each series of bends, the steel is reheated and hammered to remove the last impurities.
Shaping: bending and hardening
Once the blade has been forged, it must be shaped. The katana’s characteristic curvature is obtained through a differentiated tempering process. The swordsmiths coat the blade with a mixture of clay and charcoal. During tempering, the blade is heated and then immersed in cold water. This technique hardens the cutting edge while leaving the back of the blade more supple, creating an asymmetrical structure that increases the katana’s strength and cutting ability, and resulting in a wavy line called hamon.

This Hamon is a unique signature for each blade and gives the katana its distinctive look.
Sharpening and polishing
After tempering, the blade is meticulously polished and sharpened. This step is essential to reveal the wavy line of the hamon and to give the blade its razor-sharp edge. Polishing is carried out by specialized craftsmen, using polishing stones of different sizes to refine the blade’s surface gradually. For less expensive sharp katanas, polishing is carried out by machine.
Final assembly
The handle, called Tsuka, is then added, usually made of wood covered with ray skin (stingray leather) and wrapped in a silk or cotton Tsuka-ITO. The katana has a guard (tsuba) and is fitted with a scabbard (saya), also made of wood, which protects the blade and makes it easier and safer to carry.
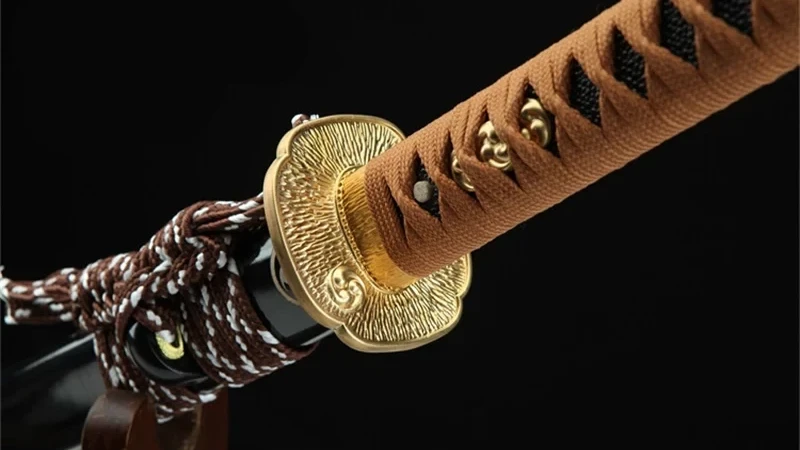
Conclusion
Crafting a katana is a long and complex process, combining tradition and innovation. Each katana is unique, resulting from hard work and mastery of the metallurgy and techniques of Japanese swordsmithing. From the preparation of the steel to the final polishing, each stage is carried out with unrivaled precision and devotion, paying tribute to a thousand-year-old tradition. These Japanese swords are not basic, but true works of art, symbolizing the culture and history of the samurai. Choose KatanaEmpire.us to acquire an authentic katana, forged with passion and swordsmanship.